3Dプリンタは近年急激に普及が進んでいる製造機器で、さまざまな造形方式があります。
今回は、数多くの3Dプリンタの中で最も歴史の深い「光造形方式」に焦点を絞り、機器の仕組みとメリット・デメリットについて探っていきたいと思います。
ぜひ導入前の検討材料としてお使いください。
目次
光造形3Dプリンタの基本的な仕組み
光造形とは
光造形とは、紫外線に反応して硬化するレジン材料を使って造形する3Dプリンティング手法です。
光造形3Dプリンタでは基本的にレジンに紫外線を照射して数十~百µmの薄いレイヤーを出力し、これを積み重ねていくことで立体的な形状を造形します。
光造形には主に3種類の造形方式と2種類の造形手法があります。
光造形3Dプリンタ|3種類の造形方式
このセクションでは、以下の3種類の造形方式について詳しく解説します。
【SLA方式】
レーザーを用いて出力箇所を点で局所的に照射する方式
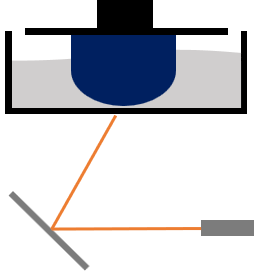
【DLP方式】
DLPプロジェクターを用いて出力箇所を面で出力する方式
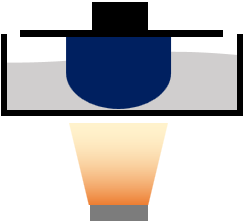
【LCD方式】
LCDディスプレイを用いて出力箇所を面で出力する方式
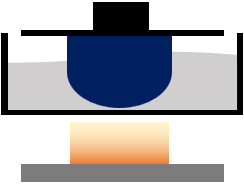
SLA方式
SLA(Stereolithography)方式は、3つの造形方式の中で最も精度の高い出力を得意とします。レーザー光で出力箇所をポイントで硬化することができるため、ピクセル数などに関係なく滑らかな表現が可能になります。
一方で、造形面積が広い出力物でも点で出力を行うため、他の造形方式と比較して造形スピードが遅くなる傾向があります。
DLP方式
DLP(Digital Light Processing)方式は、他の造形方式と比較して造形速度が高速であるという強みがあります。プロジェクター光を用いて出力面積を面で一度に照射するため、造形面積の広い出力物を短時間で硬化できます。また、DLPエンジンは約20,000時間の光源寿命を持ちランニングコストに優れています。
デメリットとして、機器導入時のイニシャルコストが比較的高価になる傾向があります。
LCD方式
LCD(Liquid Crystal Display)方式は、DLP方式と同様に面全体で出力する造形方式のため、DLP方式と同じく高速造形というメリットを持ちながら、比較的イニシャルコストが安価に導入できます。LCDディスプレイの直上で造形するため、本体サイズがコンパクトになるのもメリットの一つです。
安価なイニシャルコストの一方で、LCDディスプレイ寿命が約2,000時間と、DLP方式よりランニングコストが高価になる傾向があります。また、ディスプレイサイズの制約により造形サイズが制限されやすく、産業向けよりホビー向けに多く使われています。
SLA (レーザー光) | DLP (プロジェクター光) | LCD (パネル光) | |
---|---|---|---|
方式 | レーザー光で照射・硬化する | プロジェクターで照射・硬化する | ディスプレイで照射・硬化する |
精度 | ◎ | ○ | ○ |
造形速度 | △ | ◎ | ◎ |
光源の寿命 | ◎ | ◎ | △ |
造形サイズ | ◎ | ○ | △ |
価格帯(初期費用) | △ | ○ | ◎ |
光造形3Dプリンタ|2種類の造形手法
光造形3Dプリンタの代表的な2種類の造形手法についても解説していきます。
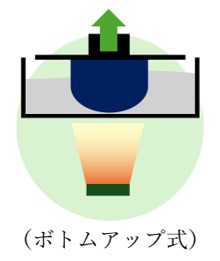
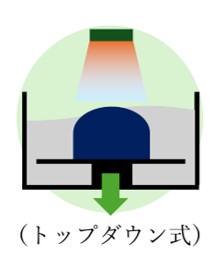
ボトムアップ式
レジンで満たしたタンクに下から紫外線の光を照射し、出力物を付着させたビルドプレートがタンクの底面から上昇していくことで層化して立体を出力します。
トップダウン式
レジンで満たしたタンクの上から光を照射し、出力物を付着させたビルドプレートが下に降りていくことで層化して立体を出力します。産業用などの大型機に多く見られる造形手法です。
光造形3Dプリンタのメリット・デメリット
光造形3Dプリンタのメリット
光造形3Dプリンタには、他の造形方式では実現できないメリットがあります。
- 表面仕上げ:
滑らかで精細な表現が可能 - 密閉性:
層と層の間も硬化されるため、完全に密閉された構造で出力が可能 - 等方性:
層と層の間が硬化されて固定されることで、縦方向と同様に横方向からの力にも強い - 耐熱性:
耐熱性に優れた材料ではHDT(荷重たわみ温度)が最高300℃まで対応 - 微細さ:
造形跡が目立たず、微細な造形が可能
光造形3Dプリンタのデメリット
一方で、光造形ならではのデメリットもあります。
- 強度:
アクリル系レジンが中心のため、靭性などの強度が出づらい - 耐紫外線:
レジンの特性上、出力物が日光などの紫外線に長時間さらされると劣化しやすい - 後工程の手間:
造形後の洗浄、硬化、サポート除去の作業に時間がかかる - 出力に苦手な形状がある:
特にボトムアップ形式の場合、液中で造形が行われるため圧力などで造形不良が発生する可能性がある
光造形と他の3Dプリンタ技術の比較
3Dプリンタには、光造形方式のほかに熱溶解積層方式(FFF/FDM)や粉末焼結方式(SLS)があり、製造業を中心とした3Dプリンタのユーザーの多くは、各造形方式のメリット・デメリットに応じて用途ごとに3Dプリンタの使い分けを行います。
3Dプリンタ技術の比較を通して、造形方式ごとの最適な用途を見つけていきましょう。
光造形方式と熱溶解積層方式(FFF)の比較
光造形方式 | 熱溶解積層方式(FFF) | |
---|---|---|
方式 | レジンに光を当てて硬化させる方式 | フィラメントを熱で融解して積層していく方式 |
イメージ | ![]() | ![]() |
造形速度 | ◎ (DLPは速い) | 〇 |
材料選択の自由度 | 〇 (アクリル系中心) | ◎ (汎用プラからスーパーエンプラまで幅広い) |
表面の綺麗さ | ◎ | △ |
造形形状の自由度 | ○ | △ |
造形物の強度 | △ | ◎ (カーボンなど高強度造形が可能) |
熱溶解積層方式(FFF)のメリット・デメリット
FFF方式は、熱可塑性樹脂のフィラメント材料を熱して融解し、ソフトクリームのように積層していく3Dプリント技術です。多くの方が一般的に3Dプリンタというと連想する造形方式になるのではないでしょうか。
FFF方式は材料の選択肢の広さが大きな強みになります。特に、ABSやPLAなどを使用することができ、汎用プラスチックからスーパーエンジニアリングプラスチックまで、工業用に最適な材質から選ぶことが可能です。また、カーボンなど高強度材料での出力に対応し、最終製品と同様の材料特性を再現できるため、産業目的で多く導入されています。造形の手軽さの面でも、モデルを配置してボタンをワンタッチで造形を開始し、サポートを除去することで完成することができます。多くの産業シーンで導入されている代表的な3Dプリンタです。
デメリットとしては、表面の積層痕が残り表面仕上がりが粗く見える特性があります。また、層と層の間が完全に結合されないため、異方性(=層と平行する方向から加わる力に弱い)があり、気密性・水密性の点では他造形方式より比較的劣る傾向があります。また、融解したフィラメントをモデル形状上になぞって出力するため、光造形のSLA方式のようにプリント速度が遅くなる傾向があります。
これらのメリット・デメリットを整理すると、FFF方式3Dプリンタの用途とは、工業用プラスチック材料を使用して部品の強度などを確かめるのに活用でき、誰でも簡単に使える3Dプリンタという位置づけになるでしょう。
光造形方式との比較
一方で光造形3Dプリンタの場合、紫外線で硬化・層化するためズレが少なく、積層痕が目立たないきれいな表面に仕上げられます。また、二次硬化の後処理加工を行うことで、出力物の層と層の間を分子レベルで結合することができ、等方性や密閉性に優れた出力が可能です。
更に、DLP/LCD方式では面で出力するため、プリント速度が高速になります。その反面、使用できる材料はアクリル系が中心になるため、熱可塑性樹脂と同質の条件を要求することが困難になります。また、高度なサポート設定や後処理工程が欠かせず、ノウハウ習得や出力完成までに手間を要する傾向があります。
光造形方式と粉末焼結方式(SLS)の比較
光造形方式 | 粉末焼結方式(SLS) | |
---|---|---|
方式 | レジンに光を当てて硬化させる方式 | 樹脂粉末にレーザーを照射して融解させる方式 |
イメージ | ![]() | ![]() |
造形速度 | ◎ (DLPは速い) | △ |
材料選択の自由度 | 〇 (アクリル系中心) | △ (ナイロン系中心) |
表面の綺麗さ | ◎ | 〇 |
造形形状の自由度 | ○ | ◎ (サポート不要) |
造形物の強度 | △ | ○ |
粉末焼結積層方式(SLS)のメリット・デメリット
SLS方式は、粉末樹脂材料にレーザー光を照射し、溶解した材料を積層していく3Dプリント技術です。
SLS方式は粉末材料の中でプリントが行われるため、粉末がサポート代わりとなり、別途サポートの設置をすることなく出力できます。このため、複雑な形状や他の造形方式で造形困難な形状の出力が比較的容易にできる強みがあります。また、他の造形方式で弱みとされる熱や紫外線に影響を受けることがほぼなく、出力物を使用する環境への留意が不要な点で特に優れている造形方式です。出力物は強度が高く、射出成型と同等の品質だと謳われており、優れた機械的特性が魅力の3Dプリンタです。
一方、使用可能な粉末材料はナイロン系が中心で、熱可塑性樹脂と同質の条件を要求することが困難になります。材料特性の選択肢も他の造形方式と比較して限定的になる傾向があります。また、出力直後の造形物の表面はザラザラとした質感になるため、後処理で加工が必要です。さらに、粉塵を取り扱うため、プリンタ設置環境に特別な集塵・換気設備を用意する必要があり、広い作業面積を要する点でデメリットに感じられることがあります。
これらのメリット・デメリットを整理すると、SLS方式3Dプリンタの用途とは、複雑な形状の部品を確実に表現でき、射出成型に代わる試作に最適な3Dプリンタという位置づけになるでしょう。
光造形方式との比較
光造形3Dプリンタの場合、材料特性の選択肢が広く、柔軟材料から高靭性・高強度材料まで使用可能です。造形物の表面品質も出力直後から最終製品並みの仕上がりで、特別な加工が必要ない点でメリットに感じていただいています。一方で、出力前にサポート設定の工程が必要なことや、出力物の紫外線への耐性が一般的に低いことがデメリットになります。
比較を経て光造形のポジションは?
上項では、FFF方式とSLS方式との比較を通して、それぞれの造形方式のメリット・デメリットを整理していきました。
造形方式ごとに一長一短があることを感じていただけたと思いますが、この比較から光造形方式の位置づけとして、筆者は精密な形状の部品を、最終製品として採用できる仕上がりで高速に造形できる(複数個同時生産が可能な)3Dプリンタであり、これを実現できる場面が最適な活用シーンになると考えています。
光造形3Dプリンタの選び方|押さえたいポイント3つ
光造形3Dプリンタは種類が多く、どれを選べばいいのか分からないという声がよく寄せられます。
そこで、3Dプリンタを選ぶ上で意識したい点を3つご紹介します。
造形に使用したい素材を確認する
光造形3Dプリンタには様々な特性を持つ材料があり、造形目的・用途に合わせて材料を選択することができます。
そのため、例えば柔らかい部品を出力したい場合は弾性レジン、熱負荷のかかる部品を出力したい場合は耐熱性レジンなど、用途に合った特性の材料をその3Dプリンタで使用できるかを確認することが大切です。
また、メーカー指定の専用レジンしか使えない機種もあるなかで、同じ特性でも異なる物性値の材料を使ってみたいという場合には、オープンマテリアルの光造形3Dプリンタを検討するのがおすすめです。
造形物のボリュームで選ぶ
光造形3Dプリンタにはデスクトップ型の小型機から産業用の大型機まであり、機種によってビルドボリュームの選択肢が広く存在します。
例えば、小さい部品の試作や小型の治具を製作する場合、比較的小型の3Dプリンタのスペックで十分ですが、自動車部品などの大型モデルの造形、または小さい部品を一面に並べて同時に複数個造形したい場合は比較的大型機が必要になります。
このように、造形できる最大サイズ(幅×奥行×高さ)を確認し、使用目的や用途に合っているかを見定めることが大切です。
表現を高める解像度で絞る
光造形方式3Dプリンタは、紫外線光やレーザーでレジンを照射して造形するため、解像度が非常に高いのが特徴です。XYの解像度(水平解像度)とZの解像度(積層ピッチ)の数値が小さいほど、細かなディテールが表現できます。
ポイントとして、選定の際にその3Dプリンタで実現したいこととマッチしているかを見極めることが重要です。
光造形のなかでも各造形方式の特徴を理解し、ニーズにあった適切なプリンタを選びましょう。
光造形3Dプリンタの価格帯
光造形3Dプリンタの価格帯は、各造形方式やプリンタ本体のサイズ/スペックにより異なります。
一般的に最も安価と言われるのがLCD方式で、続いてDLP方式、SLA方式と価格帯が変動する傾向があります。
フィギュアやモデル製作などのホビー用途向けデスクトップ型3Dプリンタの場合、10万円以下の安価なものがあります。
工業用の治具や金型、最終製品の製作を行える工業用の大型3Dプリンタの場合、機能や造形サイズにより差がありますが、価格レンジが約50万から約5,000万と非常に幅広くラインナップが揃っています。
テクノソリューションズがおすすめする光造形3Dプリンタ
テクノソリューションズでは、製造業での活用に適した高機能の産業用光造形3Dプリンタを取り揃えています。
ここで弊社イチオシの光造形3DプリンタCARIMA社「DM4K」をご紹介します!
DM4Kについて
DM4KはDLP方式を採用した、100種類以上の材料に対応したオープンマテリアルの産業用3Dプリンタです。
名前から推測いただける通り4Kの高精細出力を行うことができ、産業レベルの生産性を実現できる造形ボリュームを備えています。
特長
・超高精細
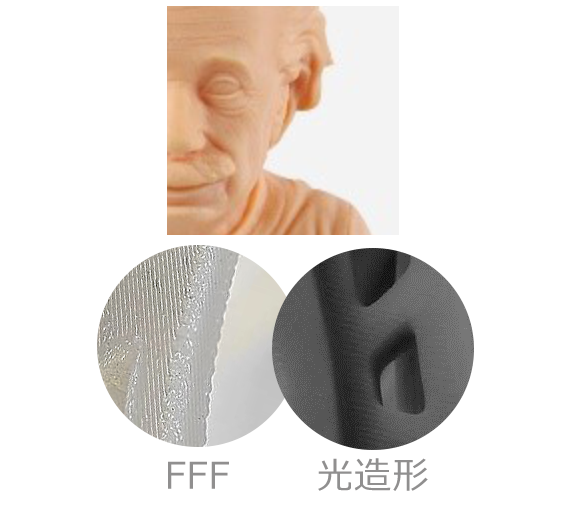
最高精度(最小値)
・XYピッチ:50μm, 65μm
・Zピッチ:30, 50, 100, 150μm
寸法精度
・±0.1mm
高解像度4Kの先進的なDLPテクノロジーにより、光造形の強みを最大限に生かした最高グレードの出力品質で造形することができます。
・産業レベルの生産性
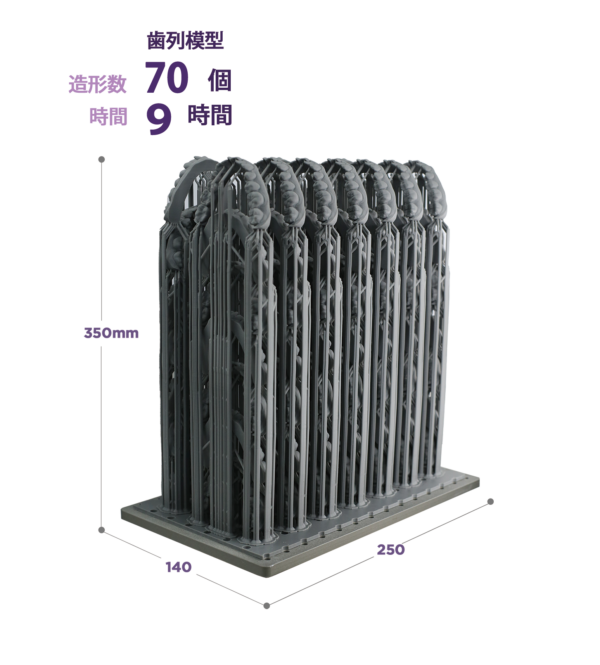
造形ボリューム(65μmの場合)
・W250 x D140 x H350 mm
最高速度
・50 mm / 時(材料の条件による)
中型サイズの部品の造形や中量生産など、造形ボリュームを生かした出力を短時間で効率的に行うことができます。
・オープンマテリアル
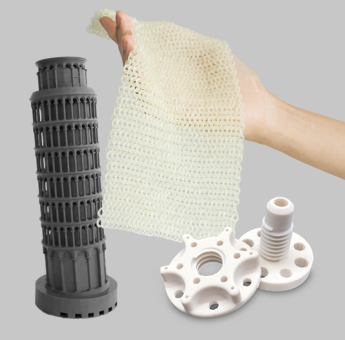
対応レジンのメーカー:8社
対応レジンの種類:100種類以上
高強度、耐熱性、難燃性、耐薬品性、生体適合性などの特性をもつレジンに対応し、試作、金型、治具、最終製品など、幅広い用途で活用いただけます。
技術
光造形の可能性を最大限に引き上げる独自技術で、かつてない3Dプリンタ体験を提供します。
CARIMA社の20年以上にわたる研究開発の経験から蓄積された確かな技術力で、ものづくりを次のレベルへ引き上げます。
・高精細な造形を実現 《解像度4KのDLPエンジン》
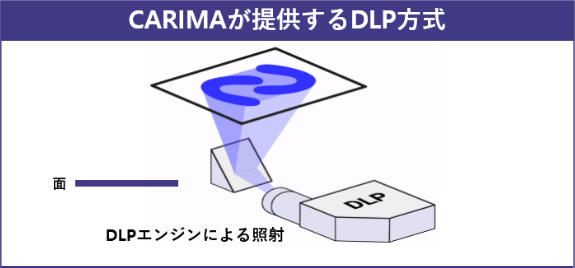
面での出力:高解像度 4K(3840 x 2160)
光源であるDLPプロジェクターが造形レイヤーを断面画像として造形面に投影し、レジンを硬化します。
造形面積の大きさに影響を受けることなく、たった数秒でレイヤーの造形が完了します。
・特許技術テンションフリーシステム搭載 《テンションフリー(TF) フィルム》
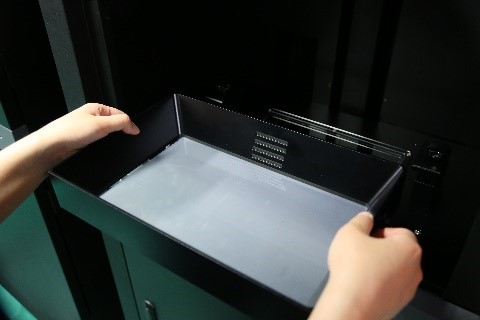
造形時の剥離抵抗:抑制率 90%
マイクロレンズアレイを通過した光を点状に集光し、造形面にピラミッド状に硬化します。フィルムと造形物の接着面積を最小化することで、造形中に発生する剥離力を抑制します。
・ヒーターシステム
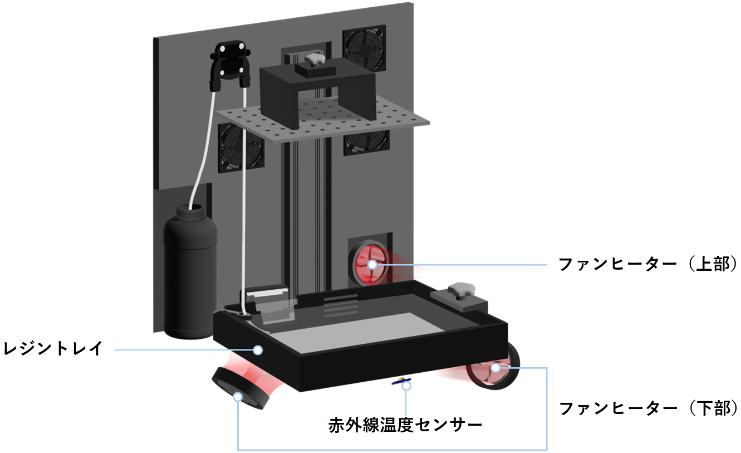
レジンの加熱温度:最高40℃
レジンタンクとフィルムを最高40℃まで加熱させるヒーターシステムを内蔵。粘度が高い高機能性レジンの出力を簡単にします。
・オートレジンフィーダー
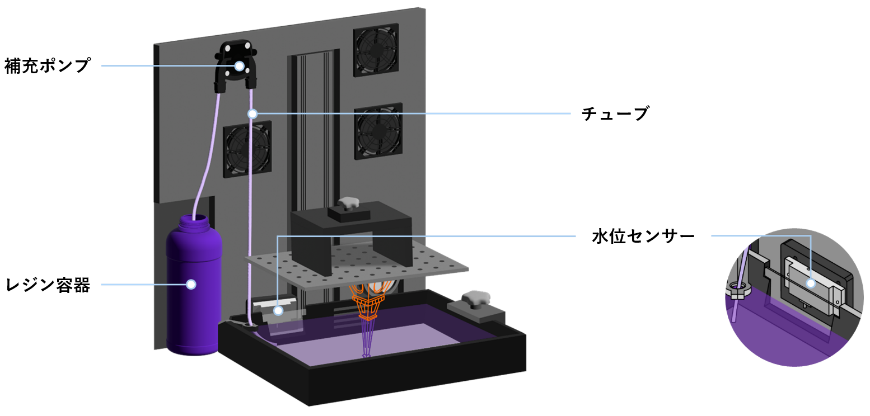
レジン管理:自動化
レジンの投入・吸引を自動で行うことで、不用意な出力停止を抑制し、レジン交換を容易にします。
材料
・高機能性材料の“超”幅広い選択肢
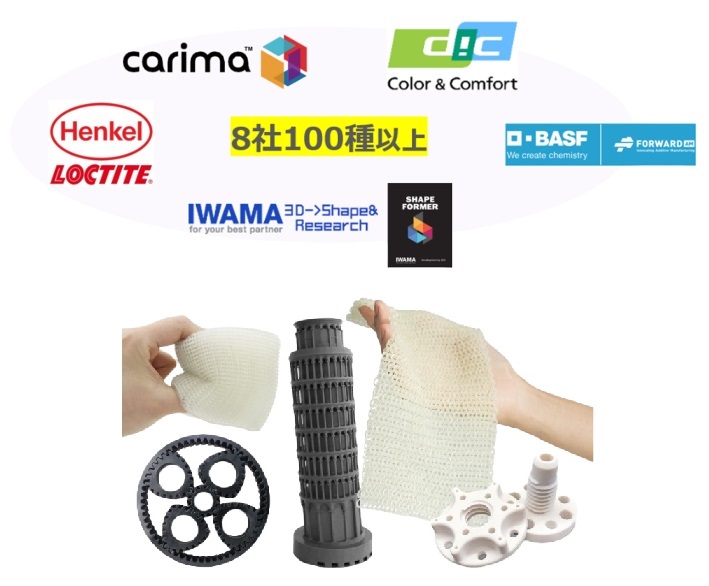
3Dプリンタ最高レベルの工業用レジン対応数
・8社
・100種類以上
高強度、耐熱性、難燃性、耐薬品性、生体適合性などの材料特性を持つ幅広い材料の選択肢をご提供します。
試作、金型、治具、最終製品など、幅広い用途で活用いただけます。
また、お客様のご希望の物性に合わせたカスタムの レジンをCARIMA社で特別にデザインし、ご提供することもできます。
【対応レジンメーカー】
CARIMA, DIC, 岩間工業所, Henkel, BASF 等
製品スペック
造形サイズ(W x D x H) | 250 x 140 x 350 mm 192 x 108 x 350 mm |
精度(XYピッチ) | 50, 65 μm |
レイヤー厚さ(Zピッチ) | 30, 50, 100, 150, 200 μm |
光源 | 385 / 405 nm UV LED |
解像度 | 4K UHD 3840 x 2160 |
設置環境 | 温度 18 – 26 ℃ 湿度 20 – 50 % |
操作 | 内臓タッチスクリーン |
本体サイズ(W x D x H) | 650 x 620 x 1734 mm |
重量 | 150 kg |
電源 | AC 100 – 200 V 50 – 60 Hz 4A |
DM4Kのユーザー事例
DM4Kは、製造業を中心とした数多くの業界・分野で活用されている3Dプリンタです。一般的に試作や金型、治具、最終製品のカスタム量産などの用途で使用されています。
ここで、実際にコンシューマー製品と工業部品で活用された事例をご紹介します。
【事例1】「透明感があるインナーリムをカスタム生産したい!」メガネメーカー
こちらの企業様は、お客様の顔の形に合ったカスタマイズのメガネを製造しているアイウェアメーカーで、3Dプリンタでインナーリムを生産されています。
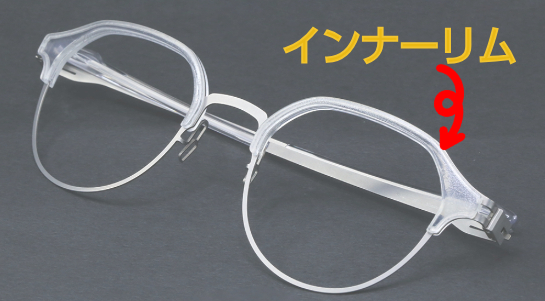
従来の3Dプリンタでは黒色や白色などの単色でしか出力できなかったことから、色の選択肢を増やし、より繊細な表現ができるという点に魅力を感じ導入していただきました。
DM4K導入により、以下を実現することができました。
- オープンマテリアルシステムの強みを発揮し、透明で光沢感のある質感を表現
- 超高精細造形の強みを発揮し、繊細なデザインの異なる種類のフレームを少量生産
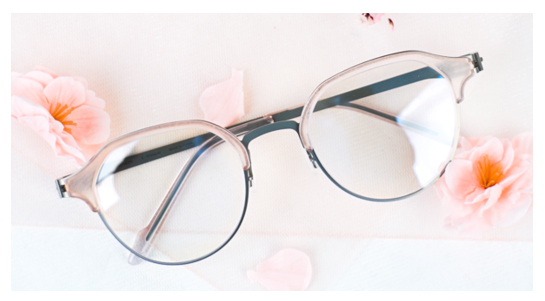
実際にDM4Kで製造されたインナーリムが採用されたカスタムメガネ「Willa (チェリーブロッサム色)」。ドイツの材料メーカー社による耐衝撃・高耐熱レジンが採用され、日常使用で心強い機械的性能を持つ。実際に販売され、2週間で完売する人気商品になった。
【事例2】「ロボット部品の製造を内製化し、製品開発期間を短縮したい!」ロボットアーム衝撃緩和パッド
こちらの企業様は、協働ロボットの安全性を分析するソリューションを開発されており、衝撃安全性テストで使用する衝撃緩和パッドの製作を行っています。
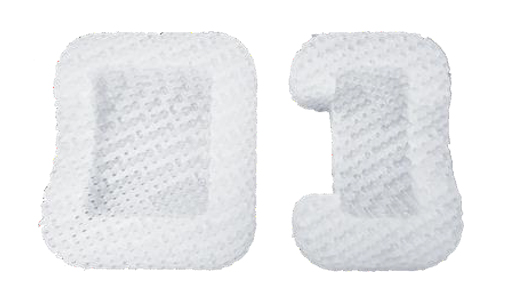
従来は衝撃緩和パッドを外注していたことから製作に時間がかかり、トータルで製品開発時間が長くなってしまうという課題を抱えていました。
DM4Kを導入することで、
- 内製化を実現し、製品の開発期間を短縮
- 軟性レジンを使用し、デザインでラティス構造を実装することで、従来のシリコンと比べて70%以上の軽量化
- ロボットの種類に合わせたカスタマイズのソリューションを提案
これらを実現できるようになりました。
機種選定で困ったら
この記事を読んで、ご自身に合った光造形3Dプリンタのイメージがついたでしょうか。
機種選定は、多くの方にとって3Dプリンタ導入における最初の関門になります。そのような時は、弊社で最適な3Dプリンタの選定をお手伝いいいたします。今回ご紹介したDM4Kを含めたくさんの機種を取り扱っておりますので、お気軽にご相談ください!
3Dプリンタ選定コンシェルジュサービス
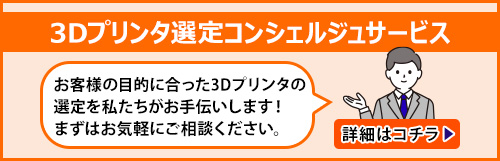
3Dプリンタ選定コンシェルジュサービスは、お客様の課題や希望をヒアリングし、導入効果が出せるような機種を選定するサービスです。
また、弊社は3D CADの取扱いもありますので、3D CAD未導入のお客様でもCAD導入からプリンタの活用までワンストップで対応することができます。
また、選定のみならず、プリンタでどのような出力ができるのかを実際に確かめたいという方向けに、ベンチマーク受託サービスも行っています。
これらのサービスにご興味を持っていただけましたら、ぜひ弊社までお問い合わせください。
問い合わせる